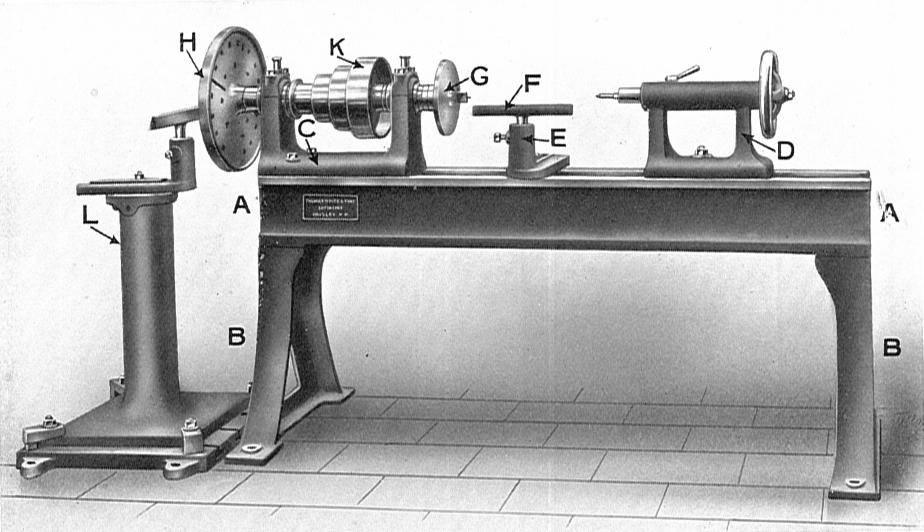
A lathe may not have a tool rest. You will need to adjust its angle to compensate for your hands' awkward position. Most tool rests have flat spots on the top bar that allow your fingers and thumbs to move back and forth. Some are adjustable and fit most lathes, while others have multiple height settings. Here are some features you should consider when buying a lathe tool rest:
Light source
If you're not familiar with the concept of a light source for a tool rest for a lathe, you're not alone. Many lathes can be equipped with overhead lighting or fixtures that attach to the ceiling, headstock or other areas. These lights are great for adding lighting to the machine, but they can be difficult to reach by operators. A tool rest with integrated lighting is the best option for larger lathes.
A tool rest for lathes includes a horizontal arm and a vertical post. On the tool arm's front side, mount a light source. Preferably an LED illumination strip. The wire 20 is used to attach the strip to an electrical power supply. A tool rest that does not include a light source can also be provided. This invention will allow the creation of a better tool rest for lathes that incorporate a light source.
Support element
The Support element of tool rest for the lathe solves several problems related to unexpected movements of the toolrest. In the prior art, the toolrest is supported by a point-to-point abutting arrangement. The friction force generated during tooling cannot support the toolrest because it must bear torque as well as axial force. This design poses safety risks. The support element for tool rest on lathe is used to protect the toolrest against torque and axial pressure generated during tooling.
A toolrest is a piece of metal that stands on its own. The bar is used to provide restraint. It may also have grooves for positioning the tool. Some models come with a handle for guiding the tool as it turns. These toolrests may be made from metal or wood. Wooden toolrests should be smoothed. However, if a support element for tool rest for lathe is not included in your budget, you can still opt for a wood one.
Adaptive device
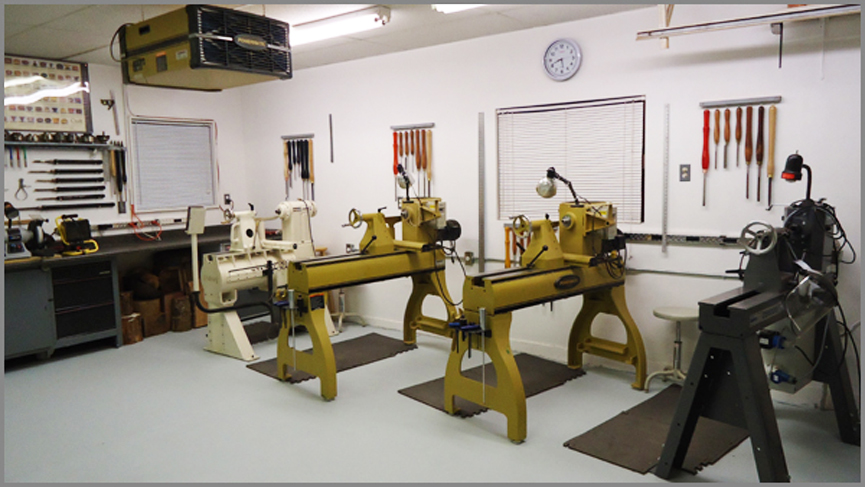
Adaptive device 100 comprises an externally cylindrical sleeve having a head and a threaded section, and a threaded portion 274 on the outer edge adjacent an end opening 150. The shoulder 140's milled portion forms a flat surface 160 which can be used to hold the set screws of 370 in the lathe holding 310. The set screw 370 is pressed against the flat side 160 to secure the adaptive device within the lathe.
The Mortimer pinrest claims it has a gated function. However, the support bar rides parallel to the tool shaft. This should allow for sufficient levering ability. This device has a very large gate, which almost certainly suffers cam locking. While this is an improvement over a standard tool rest, it offers few advantages in terms of fine tool control and motion restriction. This is not the best choice for people who require complete tool control with no compromises to precision.
Cutting tool
A cutting tool rest is a must-have accessory for any lathe user who is new to the craft. This accessory will enable you to support your lathe as closely as possible while it turns. The toolrest's body slopes backwards from the forward edge. This allows you to position your cutting tool at an optimal angle for efficient cutting. With a file, you can finish the surface of the cutting tool rest to ensure a smooth working surface.
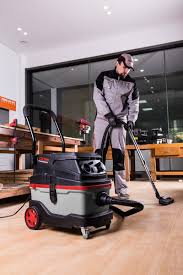
Flat spots are best for cutting tools rests for lathes. Your fingers won't rub against the flat surfaces. This is a great tool rest for handwork. It prevents your hands and fingers from slipping of the cutting blade. It is also useful for keeping the workpiece stable during high-speed turning. There are many sizes to choose from depending on your lathe. A professional can help you choose the right size for your lathe.
FAQ
Are you able to teach yourself woodworking
Doing is the best way to learn any subject. Woodworking is an art form that requires patience, practice, skill, and experience. Mastering any craft takes time.
The best way to learn how to do something is actually to do it. Start small and use what you learn.
Is it hard to start my own woodworking business?
Starting your own woodworking business isn't easy. There are many requirements and regulations that must be followed. It doesn't mean that you have to go through the entire process of starting a business. Many people opt to join existing businesses instead. This way, you only need to pay membership fees and taxes.
What kind and type of wood should i use?
Oak, maple, cherry and mahogany are the most common wood types used for woodworking. Every type of wood is different and can have a unique look and feel that will affect the final product. For example, oak tends to be darker and harder than other woods. Birch is soft and light, and mahogany is denseer and heavier. You also have the option of solid wood or veneers. Veneers can be described as thin sheets of wood that have been glued together in one layer.
How often do I need to buy new supplies
You will likely need to replace some tools over time. You'll need to sharpen your hand tools regularly if you use them. You'll also need to replace parts if you use power tools. Avoid buying too many products at once. Spread your purchases out over several months.
Can I refinish furniture that I make?
Yes! Yes! There are many methods to refinish antique furniture without hiring a professional. Here are some ideas:
Use sandpaper for removing stains and scratches. Finally, use a clean cloth or sponge to clean the surface.
Use clear polyurethane varnish. Allow to dry thoroughly before moving furniture.
Use acrylic paint to paint furniture.
You can stain the furniture instead of using paint. You can give your furniture a rich appearance with stain.
Apply shellac wax. The wax will add shine to the wood and protect it.
Can this be a way to make money?
Yes! Many woodworkers are already doing so. According to the U.S. Bureau of Labor Statistics (BLS), the median annual wage for woodworkers was $34,000 in May 2012. That's higher than the national average of $31,000 per year.
Statistics
- The best-paid 10 percent make $76,000, while the lowest-paid 10 percent make $34,000. (zippia.com)
- Woodworkers on the lower end of that spectrum, the bottom 10% to be exact, make roughly $24,000 a year, while the top 10% makes $108,000. (zippia.com)
- The U.S. Bureau of Labor Statistics (BLS) estimates that the number of jobs for woodworkers will decline by 4% between 2019 and 2029. (indeed.com)
- In 2014, there were just over 237,000 jobs for all woodworkers, with other wood product manufacturing employing 23 percent; wood kitchen cabinets and countertop manufacturing employing 21 percent. (theartcareerproject.com)
External Links
How To
How to make wooden joints
This tutorial will show how to join 2 pieces of wood together. We will use the "pockethole joint," which means that we drill holes in the wooden pieces and then glue them together. If your wood is straight and flat, this method will work well. You may want to consider other methods, such as dowel joining. Here are the steps
-
Drill Pocket Hole Joints. You will need to measure and mark the exact location of your pocket hole joint. Next, drill 3/4 inch holes in each end of each piece using a handheld drilling machine or jigsaw.
-
Sand Smooth. Sanding the wood's edges will help ensure that the joint won't split later.
-
Glue together. Apply glue to the sides of both wood. Let the wood sit for 5 minutes, then clamp it together.
-
Attach the Pieces together. After the glue has dried completely, you can clamp the pieces together until they are flush.
-
Trim Joinery. Trim any excess wood surrounding the joint once the glue has dried completely.
Allow enough space between pieces so you can turn them inside out.