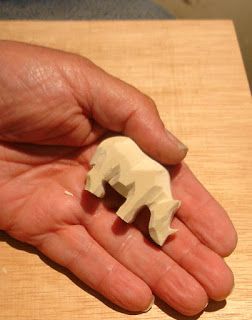
You need to be able to identify the wood species and what you should look for when carving a chain. You can also use different patterns and variations. Listed below are some helpful tips to help you get started. Once you have learned how to carve a necklace, it is time to start making your own. You can make your own chain by following these steps! You will be pleased with the results! You will be proud of the results!
Techniques
Carving a chain is an enjoyable project. It can be used as decoration, or as a gift-wrapping tool. Start by selecting a piece of square-shaped wood to begin carving. If you are an experienced carver, then basswood is the best choice. But, it can also be used to start carving. Pine wood is easier to use, but you will be frustrated until you become more proficient with the material.
Woodcarving magazines can be a great resource for learning how to carve. Each article has been written by an experienced author. These articles are written by an expert and will guide you through the entire carving process, starting with the design phase to the final step. Woodcarving is an excellent hobby for children. These guides are great resources for woodcarvers beginning to carve a chain, regardless of whether they are carving their first project or their 100th.
Wood species
There are many wood types to choose when crafting a chain. Some species are more easy than others. If you want to create intricate designs, hardwoods are the best choice. These species are also readily available in large quantities, and they are less likely burn or char. Before carving, check out the Janka hardness rating. This information can be found on Wikipedia or Bell Forest Products.
You can create a chain of wood using a sharp jack knife and a wood carving knife. You will get a cross, not a square. You can make any shape you wish, but the most effective wood chain is one of a single form. Although a chain can be made with many different shapes, it is best to stick to one shape to begin. Also, the wood must be free from mud and bark as they can dull it and cause it to break.
Patterns
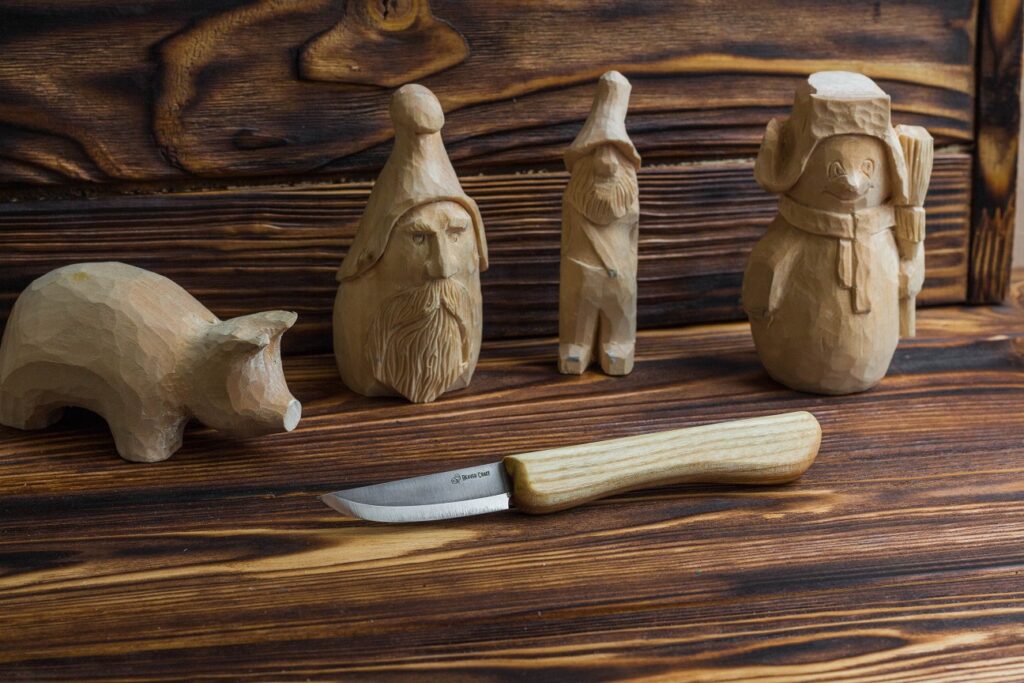
There are several different styles of wood carving and chain work is one of the more fun woodworking tricks you can do. The right example shows one-piece wood carving using a shackle with a 4-foot chain and 4" round balls. A grid pattern is used to determine the dimensions and shapes of each link. Chain patterns are made up of one-piece wood carvings. Creating a chain pattern from a grid will require a good knowledge of how to use a scrollsaw to produce these shapes.
The first step in carving a chain pattern involves hollowing out the inside of the chain links. This will allow you to create the exact form you are looking for. Once you have the basic shape you can refine the shape of your chain links and create individual profiles. Chain patterns can be square, circular, or octagonal. Beginners should stick to the round profile. You can create a functional and decorative chain by carving an octagon.
Variations
There are many different ways to carve a link. One option is to carve the profile of each link differently. The inside of the links can be carved to make your chain either square or cross-shaped. For beginners, it is best to carve a single shape. Then, you can continue to improve your chain carving skills by trying different shapes. These are some of the most common.
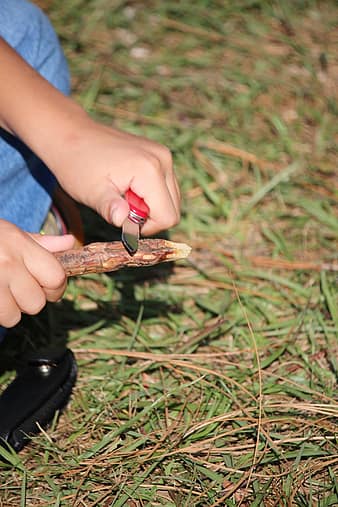
To carve a chains, you can use a knife or a strong-nosed chisel. This process is similar to carving decorative wooden vessels. The long bar is then cut into links, spiders, or ring handles. This type of carving is difficult and requires patience. One wrong move could cause the chain to break. You will also need to choose the right manager depending on the purpose of your chain.
FAQ
What kind wood should I use for my project?
The most popular types of wood used in woodworking include oak, pine, birch, maple, cherry, mahogany, teak, poplar, redwood, and bamboo. Each type of wood has its own unique characteristics that can affect the final product's appearance. Oak tends to be harder and darker than other woods. Birch is soft and lightweight, while mahogany is denser and heavier. You can also choose from solid wood or veneers. Veneers are thin sheets of wood that are glued together to form a single layer.
What is the difference in a hobbyist and professional woodworker?
Hobbyists love making things from wood while professionals are more concerned with the quality of their work. Hobbyists are proud of their creations and will often share them with family members and friends. Professionals will spend hours researching designs before they begin working on a project. They'll pay great attention to details, from choosing the most suitable materials to finishing the work perfectly.
How can a beginner woodworker make money?
Many people are starting to learn how to build furniture because they want to start an online business. However, if you're just getting into furniture building, there are other options than selling on Etsy. Sell at craft fairs or other local events. A workshop could also be offered for people who are interested to learn how they can build their own furniture. If you have the experience to be a carpenter, builder, or a designer, you may consider offering your services in remodeling homes or creating custom pieces.
Statistics
- If your lumber isn't as dry as you would like when you purchase it (over 22% in Glen Huey's opinion…probably over 10-15% in my opinion), then it's a good idea to let it acclimate to your workshop for a couple of weeks. (woodandshop.com)
- The U.S. Bureau of Labor Statistics (BLS) estimates that the number of jobs for woodworkers will decline by 4% between 2019 and 2029. (indeed.com)
- Woodworkers on the lower end of that spectrum, the bottom 10% to be exact, make roughly $24,000 a year, while the top 10% makes $108,000. (zippia.com)
- In 2014, there were just over 237,000 jobs for all woodworkers, with other wood product manufacturing employing 23 percent; wood kitchen cabinets and countertop manufacturing employing 21 percent. (theartcareerproject.com)
External Links
How To
How to make wood joints
This tutorial will demonstrate how to join two pieces together of wood. We'll use the "pocket hole joint," which means we drill holes in the wood and then glue them together. This method is great if your wood's straight and smooth. Dowel joinery might be a better option if your wood is not straight or flat. Here are the steps
-
Drill Pocket Hole Joints. Start by measuring and marking the spot where the pocket hole joint will be placed. Next, drill 3/4 inch holes in each end of each piece using a handheld drilling machine or jigsaw.
-
Sand Smooth. The wood's edges can be sanded to prevent splitting.
-
Glue Together. Apply glue to the sides of both wood. Let the wood sit for 5 minutes, then clamp it together.
-
Secure the pieces together. After the glue has dried properly, clamp the pieces together to make sure they are flush.
-
Trim Joinery. Trimming the joinery after glue has completely dried.
To be able to turn the pieces inside-out, leave enough room between them.