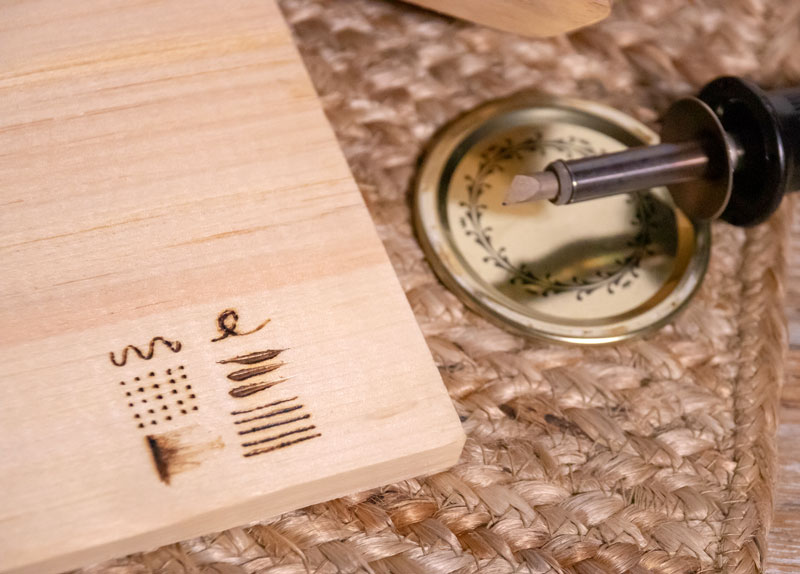
You have many options when it comes to wood-burning art. For example, basswood is a good choice if you want a clear color with no disturbing grains. Unfortunately, this wood is often very expensive and hard to find in the size you need. Birchwood is another popular wood that is light in color and has a fine texture.
Preparing wood in preparation for pyrography
Preparing the wood that you will use is the first step of pyrography. Dark wood won't display the art as well as wood with a prominent grain pattern. For pyrography, it is a bad idea to use resinous woods or uneven timber. Make sure to clean the wood before you start burning it. After you've prepared the wood for burning, it is ready to go!
Shellac can be used temporarily to seal pyrography designs. Shellac can cause wood to turn yellow when heated and should not be used for cutting boards or coasters. Paste wax can be an affordable alternative to shellac. Paste wax is a natural, smooth finish that can be applied to wood. It gives it a sheen. It is easy to apply, and it looks natural.
Wooden design.
Make a sketch to show how you want to design your wood burning art. This can also be done with a ruler, pencil, eraser and ruler. Premade stencils are particularly useful. Wood burning sets for beginners can be purchased that include all necessary tools. Here are some wood-burning design ideas to help you get started.
You can also paint directly on the burned art. You can use either a pointed pen, or a flat pencil. Be careful to not burn too deep or you will end up with holes in the work. You can also add shading to your wood-burning art. When you're finished, you can also apply color to it. Once the wood is cooled, you may add shading to your woodburning artwork.
Creating Lichtenberg burns

It is a very interesting art form to create Lichtenberg burns. Using a microwave transformer and a high voltage, you can create branching electrical discharges. Lichtenberg first discovered Lichtenberg figures in 1777. Lichtenberg wood burning has become an increasingly well-known form of art because it uses fragmental wood. Here are some tips to make these figures.
Safety equipment is required before you can begin. High-voltage transformers are commonly used to power appliances and neon signs. These transformers have a higher chance of electrocution due to their vulnerability to live wires and unprotected. You also need to wear gloves and be careful when using a Lichtenberg device. You should also wear rubber gloves. Use gloves only one hand at a while, and keep the other behind you. Even though you might be electrocuted even if your hand touches an energized electrode for a while, it won’t cause your heart to stop beating. A second thing you should remember is to always have someone there to assist you with a Lichtenberg unit. This second person will be there to turn off the electricity if you get electro
First, you need a power source. A Lichtenberg device requires a high-voltage electrical source. Burning wood can only be done with an electrical current of at least 2,000 volts. This is why most woodworking organisations forbid the practice. Safety is paramount, no matter how you create a Lichtenberg-like figure. Protective clothing and gloves are essential when working with electric current. Before you contact the outlet, make sure to double-check it.
Using a stencil
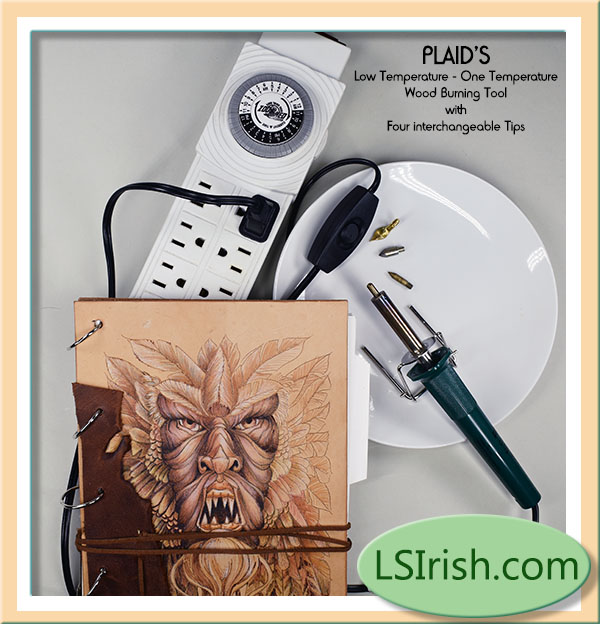
A stencil can be used to create intricate woodburning designs. The stencil allows you to trace the design on graphite paper and then transfer it to wood. You can use the stencil as a guide to your hands and eyes. However, the final design is up to you. You can use a pencil or a pen to trace a design, but it is best not to hold the stencil and wood together.
First, sand your wood so that you can burn the image. Once the wood has been sanded you can begin designing. You will need to apply some pressure to transfer graphite onto the wood to make sure that the design is clear. When you're done, you'll have to remove the tracing paper.
FAQ
How long does it take to finish a piece of furniture?
It depends on the type and complexity of your design as well as the amount of finishing that you use. Hardwoods require more care than softwoods. Hardwoods also tend to be more expensive than softwoods. However, they are stronger and more resistant to moisture. The typical time taken to finish a piece furniture takes anywhere from one to three month.
How much does a hobbyist need to invest in getting started?
It is likely that you will need some capital in order to buy the required tools and supplies if your goal is to open your own woodworking business. The best place to start is by buying a small drill press, circularsaw, circular saw or sanding machine. These items are affordable so you won’t break the bank.
Does it take a genius to make woodworking work?
No. No. Woodworking isn't rocket science. Anyone can learn to use basic powertools and techniques to create beautiful work of art.
What material would your recommendation be to learn woodworking?
You can start with softwoods like pine or poplar. You will feel more comfortable with these softwoods, so you can move onto hardwood.
What is the minimum amount I will need to start?
Because every project is unique, there aren't exact numbers. But if you want to get an idea of how much money you'll need, consider these factors:
-
Material costs
-
Tools and equipment
-
Time spent working on the project
-
Hourly rate
-
What profit are you expecting to earn?
-
Whether you plan to hire help
Start small, if possible. You can make simple boxes or picture frames if you're just getting started. As you gain experience, you'll be able to tackle more complex projects.
What kind of wood should I use?
Woodworking is a popular job that involves oak, pine and maple. Each wood variety has distinct characteristics that influence the final product's look and feel. Oak is a darker wood and tends to be more durable than other types. Birch, which is lighter and soft, is more heavy than mahogany. There are two options: solid wood and veneers. Veneers are thin sheets or wood that are glued together into one layer.
Statistics
- Woodworkers on the lower end of that spectrum, the bottom 10% to be exact, make roughly $24,000 a year, while the top 10% makes $108,000. (zippia.com)
- If your lumber isn't as dry as you would like when you purchase it (over 22% in Glen Huey's opinion…probably over 10-15% in my opinion), then it's a good idea to let it acclimate to your workshop for a couple of weeks. (woodandshop.com)
- Overall employment of woodworkers is projected to grow 8 percent from 2020 to 2030, about as fast as the average for all occupations. (bls.gov)
- Average lumber prices rose about 600 percent between April 2020 and May 2021. (familyhandyman.com)
External Links
How To
How do you measure wood accurately?
We use several methods to measure wood. A digital caliper is a tool that measures distances. We also use a laser level to ensure your work surface flattens.
Two jaws can be opened and closed on a digital caliper. The one jaw holds the object to be measured, while the other measures distance between them. The digital scale is perfect for measuring tiny distances such as wood thickness.
Laser levels feature an infrared-light beam that projects lines across the floor. The laser emits red dots on the line. You can check if the surface is level by looking down at the line. For larger surfaces, laser leveling is the best method of checking accuracy.
Bubble levels look similar to a compass. The center of the device contains a bubble. The device will indicate whether the surface is level as long as it is centered. Bubble levels are good for checking the accuracy of smaller areas.